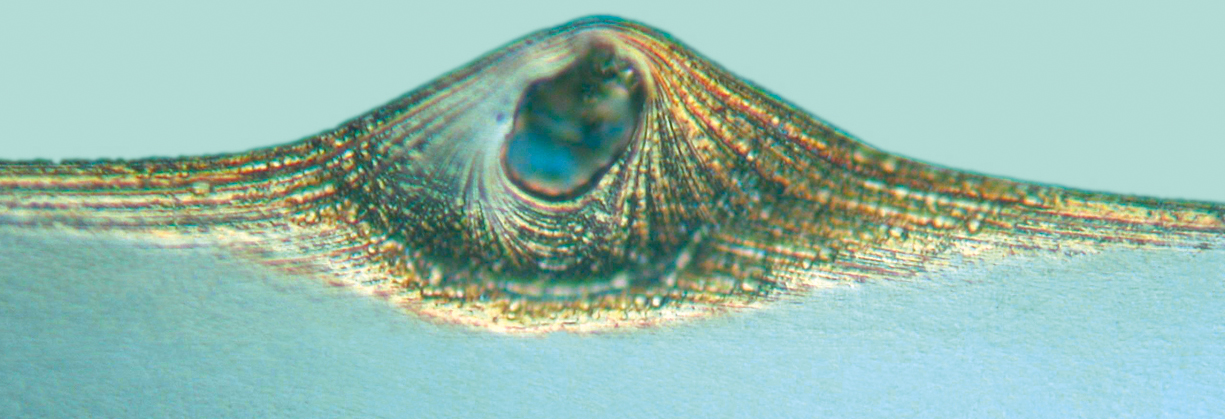
Trotz moderner Technik und präziser Fertigungsprozesse sind Beschichtungsfehler eine häufige Herausforderung – sowohl während der Produktion als auch beim Einsatz im Feld. Ein Schadensfall an organischen oder galvanisch beschichteten Bauteilen führt nicht nur zu hohen Kosten und Imageverlusten, sondern kann auch Risiken für Umwelt und Sicherheit darstellen. Wenn keine offensichtlichen Ursachen gefunden werden, sind detaillierte Analysen entscheidend, um Probleme nachhaltig zu lösen.
Mit unserer jahrelangen Expertise in chemischer, metallographischer und physikalischer Analytik sowie umfassendem Know-how im Bereich der Beschichtungen, ihrer Materialeigenschaften und Anwendungsfelder helfen wir Ihnen, die Ursachen von Beschichtungsschäden bzw. und Lackierschäden eindeutig zu identifizieren und wirksame Maßnahmen zu ergreifen.
Mit unserer langjährigen Erfahrung in chemischer, metallographischer und physikalischer Analytik unterstützen wir Unternehmen dabei, Beschichtungsfehler gezielt zu analysieren und zu beheben. Unsere Experten identifizieren die Ursachen und entwickeln individuelle Maßnahmen, um zukünftige Fehler zu vermeiden.
Unsere Untersuchungen decken eine Vielzahl möglicher Schadensursachen ab, darunter:
Häufig wirken mehrere Faktoren zusammen. Unsere Analysen identifizieren auch komplexe Wechselwirkungen, um klare und nachhaltige Lösungen zu erarbeiten.
Jeder Beschichtungsfehler ist einzigartig und erfordert eine angepasste Vorgehensweise. Unser Team bietet Unterstützung bei einem breiten Spektrum von Beschichtungsproblemen – von Holz- und Wandfarben über hochspezialisierte Lacke in der Automobilindustrie bis zur galvanisierten Kolbenstange.
Wir setzen auf fortschrittliche Mess- und Analysetechniken. Dazu gehören unter anderem:
Unsere Analytik deckt nicht nur die Ursachen von Beschichtungsfehlern und Schadensfällen auf, sondern liefert auch Handlungsempfehlungen zur langfristigen Verbesserung Ihrer Prozesse.
Schadensbild: Die UV-gehärtete Beschichtung lässt sich mit einem Tape ohne weitere Krafteinwirkung vom Substrat abziehen.
Analysierter Fehler: Es wurden keine benetzungsstörenden Substanzen auf dem Substrat detektiert. Allerdings zeigt die infrarotspektroskopische Analyse des Doppelbindungsumsatzes, dass die Beschichtung nicht bis zur Grenzfläche zum Substrat durchgehärtet ist.
Lösungsansatz: Im Prozess wurden UV-Lampen teilweise ausgetauscht, wobei die Ersatzlampen nicht optimal für den vorliegenden Lack geeignet sind. Es bedarf dem Einsatz alternativer Strahlungsquellen für den Härtungsvorgang.
Schadensbild: Zinkstaubfarbe an einer Produktionsanlage blättert massiv ab und stört den Produktionsprozess.
Analysierter Fehler: Mittels thermogravimetrischer Analyse wurde nachgewiesen, dass die eingesetzte Zinkstaubfarbe zu deutlichem Bindemittelabbau unter Temperatureinwirkung neigt und somit für die Produktionsanlage im vorgegebenen Temperaturbereich ungeeignet ist.
Lösungsansatz: Aufgrund der thermischen und chemischen Belastung in der Produktionsanlage ist die Einführung eines stabileren Lacksystems mit geeigneten Belastbarkeitsgrenzen zu empfehlen.
Schadensbild: Der Klarlack ist deutlich weicher als üblich und neigt zur Ausbildung von Abdruckstellen bereits bei leichtem Andrücken.
Analysierter Fehler: Mittels infrarotspektroskopischer Analyse wurde gezeigt, dass das Mischungsverhältnis von Stammlack und Härter des 2K-Klarlackes deutlich außerhalb der Spezifikation liegt.
Lösungsansatz: Der 2K-Mischprozess war nicht richtig eingestellt und muss nachjustiert werden. Die prozessbegleitende analytische Kontrolle erlaubt eine Sicherstellung des richtig eingestellten Mischungsverhältnisses.
Schadensbild: Scheinbar zufällig auftretende Enthaftungserscheinungen der Beschichtung auf massiven Metallteilen.
Analysierter Fehler: Die Beschichtung weist stark unregelmäßige Schichtdicken auf. Im Bereich der höheren Schichtdicken wurden mittels Gaschromatographie-Massenspektrometrie signifikante Mengen an Restlösemittel detektiert. Zusätzlich wurden mittels Dynamischer Differenzkalorimetrie eine für die vor-liegende Anwendung zu niedrige Glasübergangstemperatur sowie Hinweise auf Nachhärtungsvorgänge festgestellt.
Lösungsansatz: Der Lack muss innerhalb der vorgegebenen Schichtdickenspezifikation appliziert und optimal ausgehärtet werden.
Problemstellung: Abplatzung der chemisch Nickel-Schicht und Korrosionserscheinungen am Grundwerkstoff bei einem sicherheitsrelevanten Bauteil für Windkraftanlagen. Korrosion ist erst nach der Abplatzung entstanden, führt jedoch zu einer erschwerten Ursachenermittlung.
Analysierter Fehler: Erkennbare Deformation der Nickelschicht und des Substrates durch äußere mechanische Belastung
Ursache: Es ist davon auszugehen, dass die gewählte Beschichtung nicht an die mechanische Belastung beim Einsatz angepasst wurde bzw. überdurchschnittlich hohe Kräfte auf das Bauteil gewirkt haben.
Problemstellung: Hohe Ausschussquote bei der Beschichtung von Kunststoffbauteilen im Automobilbereich.
Vorgehen: Beurteilung der Fehler und Eingruppierung anhand metallographischer Untersuchungen. Darauf aufbauend erfolgt die Vor-Ort-Analyse des Produktionsprozesses bis hin zur Begleitung und Beurteilung der Anlagenwartung. Korrelation der Ergebnisse und Erarbeitung von Abhilfemaßnahmen.
Ergebnis: Aufgrund verschiedener Fehlerbilder werden unterschiedliche Maßnahmen mit einer entsprechenden Priorisierung zur Umsetzung aufgezeigt, um die Ausschussquote zu reduzieren.
Problemstellung: Vielzahl an Fehlerbildern an beschichteten Kunststoffbauteilen im Lüftungsbereich.
Vorgehen: Fehleranalyse durch metallographische Zielpräparation und Beurteilung des Produktionsprozesses
Ergebnis: Vielfältige Ursachen führen zu verschiedensten Fehlerbildern. Ein wesentlicher Aspekt zeigt sich jedoch im Kunststoff. Unzureichende Spritzgussparameter und nicht angepasste Spritzgussmaschinen verursachen Inhomogenitäten im Bauteil, die sich in der klassischen Kunststoffgalvanik nicht beschichten lassen.
Problemstellung: Verchromte Spezialherdplatten weisen Korrosionserscheinungen auf.
Analysierter Fehler: Verstärkter Angriff der Chromschicht führt zur Ausbildung von Korrosion und somit zum Versagen des Bauteils.
Ergebnis: Untersuchungen der Schichtoberfläche deuten auf einen chemischen Angriff der Chromschicht hin, verursacht durch chloridische Lösungen. Durchgängige Störungen im Schichtverbund sind nicht erkennbar, so dass ein Beschichtungsfehler ausgeschlossen werden kann.