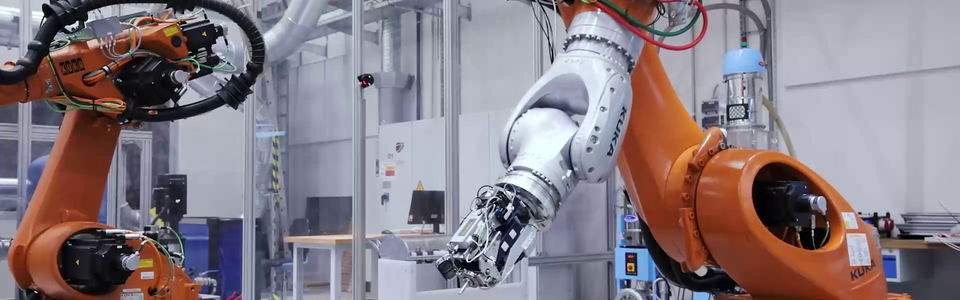
Enabl3D kombiniert Eindringprüfung, Prozessmonitoring und µCT, um Qualitätseigenschaften schnell und zuverlässig direkt am fertigen Bauteil zu erfassen. Die neue Methode zur Qualitätssicherung soll die Wirtschaftlichkeit bionischer Metall-3D-Druck-Leichtbauteile steigern.
Additive Fertigung oder 3D-Druck kann den CO2-Ausstoß insbesondere in der Luftfahrt nennenswert senken. Hier können bionische Metall-3D-Druck-Leichtbauteile den Kraftstoffbedarf reduzieren und Materialbedarf wie Ausschuss gleichermaßen minimieren. Der großflächige Einsatz erfordert jedoch eine hohe Wirtschaftlichkeit und zuverlässige Qualität. Hier setzt das Projekt Enabl3D an.
Zur Entwicklung einer effizienten Qualitätssicherung haben die Projektpartner Fraunhofer IAPT, VisiConsult GmbH und Imprintec GmbH drei Prüfverfahren kombiniert.
In dem Projekt gelang die Entwicklung eines Verfahrens zur Qualitätsbewertung additiv gefertigter Bauteile: Das In-Situ-Monitoring des Fraunhofer IAPT identifiziert Bereiche, die mit CT-Scans untersucht werden müssen. Die CT-Scans erfolgen robotergestützt und ermöglichen die Extraktion der kritischen Bauteilfehler. Die Eindringprüfung bestimmt lokal die mechanischen Bauteileigenschaften. Ergänzt um Simulationen erlaubt die Kombination der drei Prüfverfahren Rückschlüsse auf die individuellen Bauteileigenschaften.
Im Teilprojekt zur »Integration von Härtemesstechnik« haben das Fraunhofer IPA und die Firma Imprintec GmbH 6-Achs-Industrieroboter angebunden. Es wurden erste erfolgreiche Tests an Bauteilen, auch aus der Serienfertigung, durchgeführt. Dabei konnten die Partner zielführend ihre Kompetenzen im Bereich Fertigungstechnik, Messtechnik und Integration neuer robotergeführter Werkzeuge und Messtechnik einbringen.
Die Ergebnisse ebnen der Additiven Fertigung den Weg in neue Anwendungsbereiche im Bereich der Serien- oder Einzelteilfertigung in Luftfahrt, Automobil- und Medizintechnik.