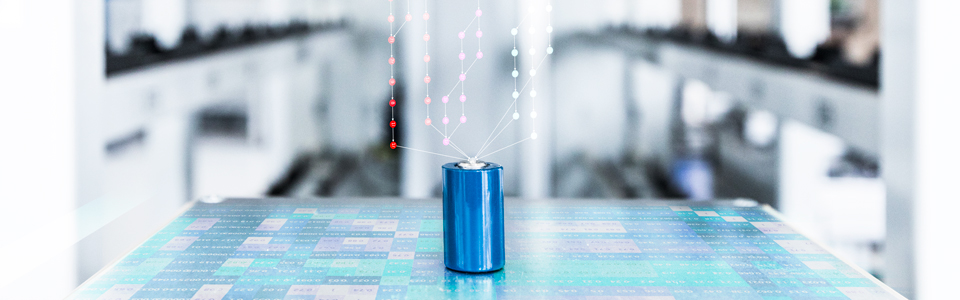
Drive batteries account for a large proportion of added value in the manufacture of electric cars. The battery cell is a key technology and thus of central importance. Manufacturing battery cells in Europe and Germany in the future is both a political aim and an economic necessity. This can only be attained by planning and constructing climate-friendly giga-factories for producing high-quality battery cells. Digitizing the value chain end-to-end will not only provide decisive competitive advantages but also be a unique selling point. At the Center for Digitalized Battery Cell Manufacturing, methods and tools for this are being developed and extensively tried and tested on a laboratory line.
Digitizing the entire value chain in battery cell production is one of the tasks of the Center for Digitalized Battery Cell Manufacturing (ZDB). Research services support the certification and scaling of existing (lithium ion) and future battery cell concepts and manufacturing processes. The focus is always on stabilizing and improving product quality while considering strict economic and ecological constraints. To achieve this, ZDB optimizes individual production processes and complete interlinked production lines as well as higher-level process and building infrastructures. In the future, the Center for Digitalized Battery Cell Manufacturing at Fraunhofer IPA will contain an entire, fully digitized production chain for lithium-ion battery cells.
Our laboratory equipment maps large parts of the value chain of a battery cell production. Using our digitization tools, we will gladly assist you with everything from process development & optimization right up to characterization and (post-mortem) analysis of different battery systems.
In the future, a pilot line for assembling round cells will be available at our institute for producing customer-specific round cells on a prototype basis.
Simulation tools
Equipment
Equipment
Equipment
Equipment
Equipment
Equipment
Equipment
Equipment
Equipment