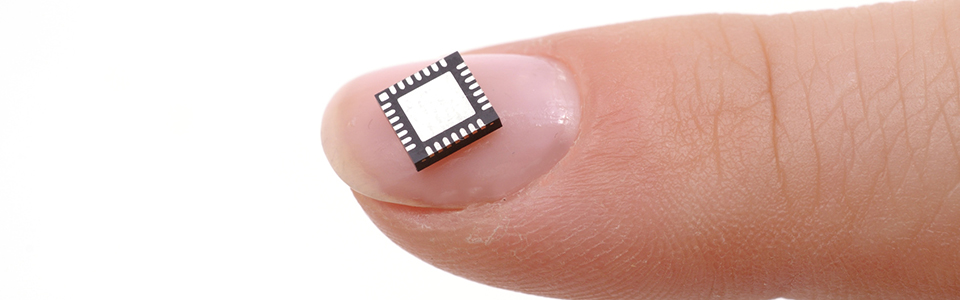
The first PCs which came onto the market in the 1980s were bulky objects the size of a suitcase and very uncomfortable to use. Today, any smartwatch is capable of much, much more than these dinosaurs could ever do. Miniaturization has since reached a level no-one would have believed possible a decade ago. A transistor on an integrated circuit is smaller than any battery, sensors are just a few millimeters in size and some screws are so small that you need a magnifying glass to see them. There are pacemakers that are as small as a pill and single-use laboratories complete with pumps, valves and conduits which fit onto a silicon chip. Tiny pico satellites not much bigger than a bit of butter are being launched into space. The tendency to miniaturize things as much as possible is particularly evident in the world of electronics and microsystems. “Miniaturization places enormous demands on production processes and often requires completely new concepts”, says Dr. Udo Gommel, who was head of the business unit until February 2016. Above all: everything must be scrupulously clean. If a speck of dust is sufficient to cause the complete failure of a component or even of a whole system, then cleanliness has to be given top priority. Such degrees of miniaturization also demand new processing and assembly technologies. For example, standard tools and methods are rarely suitable for handling these tiny delicate components. Adhesives used in joining processes also need to be applied extremely accurately.
The staff at the business unit “Electronics and Microsystems” rise to the challenges related to the manufacture of such products. In this way, they make a major contribution towards solving industry’s manufacturing issues. On their own or together with partners, they also develop concepts for products, such as a compact radar scanner realized within the scope of the Fraunhofer Alliance. The scanner sees through visible obstacles and reproduces sharp images despite dusty, smoky, foggy or rainy conditions.
To manufacture structures as fine as a human hair or process miniature components, a clean controlled environment - usually a cleanroom - is required. Fraunhofer IPA researches into and evaluates connections between the contamination behavior of production equipment and the achievable quality of manufactured products. To enable this, in addition to a wide range of analysis equipment, Fraunhofer IPA has the world’s largest ISO Class 1 cleanroom research laboratory with a laminar displacement airflow at its disposal. Over 6 meters high, it has a floor surface area of around 150 square meters. Designed for heavy duty machinery, it is not only used to conduct tests on and optimize very small end-products but also on a combination of typically large and heavy manufacturing equipment/systems weighing together up to almost 40 tons.
One cubic meter of air in the cleanroom contains a maximum of 10 particles sized 0.1 micrometers. By comparison, a cubic meter of typical air in a town contains 10¹³ particles.
The institute uses the latest equipment, such as scanning electron microscopes, micro computer tomographs and mass spectrometers, to measure contamination on components and investigate and compare the efficiency of different cleaning methods. It is therefore no wonder that experts from Stuttgart are on important committees responsible for standardizing cleanliness and cleaning methods.